Corrosion of reinforcement is a one of the most important causes of deterioration of concrete. In this article, we try to explain what is Corrosion of reinforcement in concrete and what are the causes of it.
So Please read the article till the end, and if you like or dislike please comment.
Table of Contents
What is Corrosion of Reinforcement
Corrosion of reinforcement is a very complex process. It includes chemical, electrochemical and physical processes.
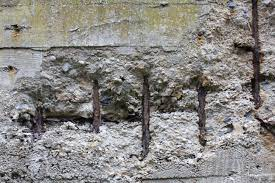
When reinforcement steel is corroded, iron oxides are produced that are 2 to 4 times the size of the corroded steel. Hence, in concrete, high stresses are generated around the steel bars which leads the cracks in concrete and at end concrete breaks.
Also, corrosion reduces the cross-section of the reinforcement bar, thereby reducing its ability to withstand tensile forces.
Also Read: Pre and Post Anti-termite treatment
For the corrosion of reinforcement, an electrochemical cell must first be formed. This cell has two electrodes – anode and cathode. Both these electrodes are separated by an electrolyte and connected in an electric circuit.
The part where more oxygen is concentrated on the surface of the reinforcement bar becomes the cathode. And the part where less oxygen is concentrated on the surface of the reinforcement bar becomes the anode. Concrete always contains some moisture which acts as an electrolyte.
Also, electrochemical cell is formed due to salt concentration in the water which is held by concrete voids. The part where more salt is concentrated becomes the anode, while the part that has less salt concentrated becomes the cathode.
The Anode and Cathode have a potential difference. Hence, the steel is further oxidized in the presence of water and oxygen near the anode to form iron oxide.
Near the anode, + charged ferrous ions (Fe++) move into the solution, While, – charged free electrons (e-) pass through steel reaches the cathode. These free electrons (e-) combine with water and oxygen and formed Hydroxyl ion (OH-) near the cathode.
This Hydroxyl ion (OH-) combines with Fe++ ion and formed Ferrous Oxide Fe(OH)2. And again oxidation of ferrous oxide formed ferric oxide Fe(OH)3 which leads the corrosion of reinforcement.
These processes can be illustrated as follows.
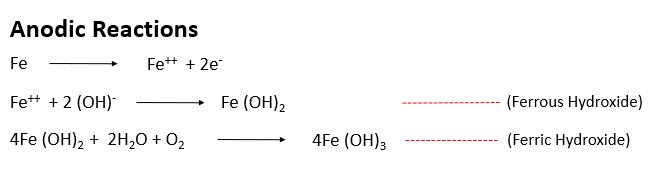
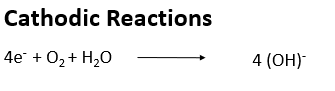
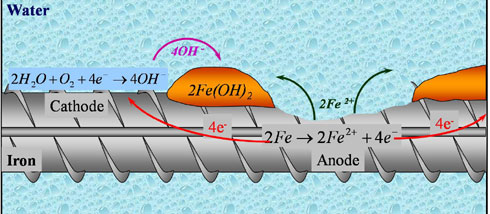
Also Read: Methods to Repair leakage of toilet and Bathrooms
Causes of Corrosion and Preventive Measures
- Cracks in Concrete
- Presence of moisture
- Permeability of concrete
- Carbonation
- Chlorides
- Sulphate Attack
- Alkali Aggregate reaction
- Inadequacy of cover
1. Crack in Concrete
Due to Cracks in concrete, water and oxygen enters into the concrete leads the corrosion of reinforcement. In moderate condition, width of cracks should not be grater than 0.30mm in inner structural members, and 0.20mm in outer structural members.
For More Details See: Causes of Cracks and Remedial Measures
2. Presence of moisture
Presence of moisture is necessary to start a corrosion in reinforcement. Because, Moisture is act as a electrolyte in electrochemical cell.
3. Permeability of concrete
Permeability of concrete is also one of the main reason for corrosion of reinforcement in concrete. Permeable concrete allows entry of water and oxygen into the concrete which leads the corrosion
0.1 increase of water cement ratio, increases the concrete permeability 1.5 times. Improper curing increase the concrete permeability 5 to 10 times. While improper compaction increase the concrete permeability 7 to 10 times.
4. Carbonation
Carbon dioxide (CO2) of atmosphere enters into the concrete and combines with calcium hydroxide to form calcium carbonate, which is soluble in water. This process is called carbonation.
Carbonation reduces the alkalinity of concrete and reduces its resistance to corrosion. Minimum 20 mm cover is required in RCC to prevent corrosion of reinforcement due to carbonation.
Also Read: Strengthening of Existing RC Slab
5. Chlorides
Cement paste of concrete, create a layer of gamma iron oxide around the reinforcement bar which prevent steel against the corrosion. But, Chlorides ion break the layer which leads the corrosion of reinforcement into the concrete.
For RCC the chloride content in the aggregate should not exceed 0.05% and the calcium chloride content in the mixing water should not exceed 1000 PPM. The content of calcium chloride used as admixtures in concrete should not exceed 1.5%.
6. Sulphate attack
Soluble sulphates like sodium, potassium, magnesium, calcium, etc. present in water, soil or bricks. These sulphates combine with Tricalcium aluminate (C3A) and lime of cement to form a ettringite which is very large in size. So the concrete cracks and the steel bars gets rusted.
To Prevent the effect of sulphate attack,
- Grade of concrete should not be less than M20
- Use Sulphate resisting cement.
- Water cement ratio should not be greater than 0.45
- Water used for concrete should be free from sulphate or sulphate content not greater than 500 PPM.
7. Alkali Aggregate Reaction
OPC Cement contains alkalis like sodium oxide (Na2O) and potassium oxide (K2O). These alkalies react with some reactive aggregates (traps, andesites, phyolites, silicious limestone, dolomite) which is called alkali aggregate reaction. This process causes the concrete to expand and crack.
To prevent the effect of alkali aggregate reaction
- Reactive type aggregate should not be used.
- Alkali content in cement should not exceed 0.6%.
- Portland Pozzolana cement should be used.
Also Read: What is Monolithic Construction Technology
8. Inadequate concrete cover
If the concrete cover is inadequate, sea water, moisture, carbonation will cause steel to corrode.
The following are recommended covers in concrete as per IS 456–2000.
- Cover should not be less than the diameter of the bar.
- Cover in column should not be less than 40mm.
- Minimum cover thickness in concrete in any case not less than 20 mm.
- Should not be less than 50 for footing.
Apart from this following measures are also taken to prevent corrosion of steel.
- Application of protective coating
- Modification of concrete
- Change in Metallurgy of steel
- Cathodic protective system.
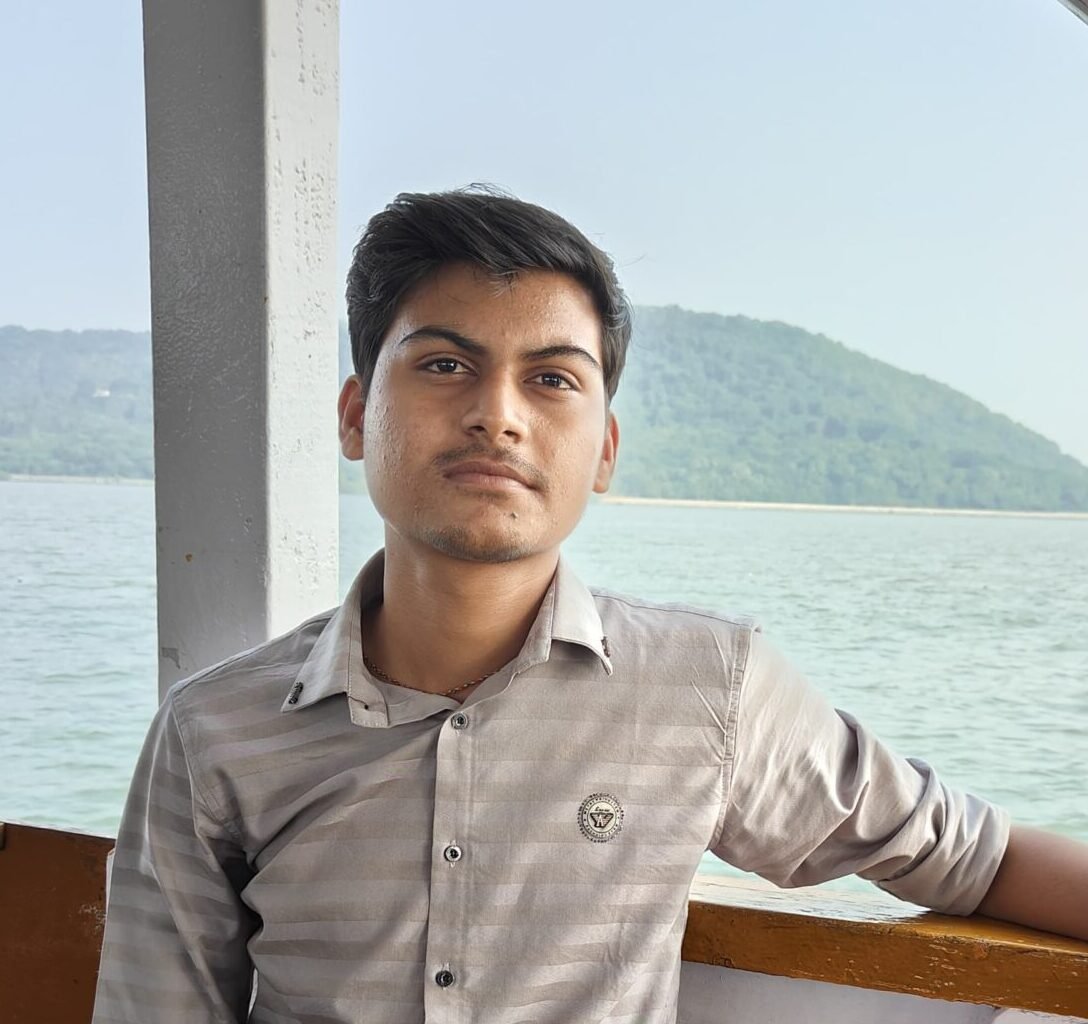
I am a Professional Civil & Structural Engineer having more than 4 years of experience in Engineering, Procurement and Construction industry. Here i sharing the latest updates of EPC Projects and Construction News.