In this article, we share the information of modular construction such as what is modular construction, advantages and disadvantages of modular construction buildings, types of modular construction, etc.
So, if you get any valuable information from this article then please share it with your friends, Let’s start.
Now a day, modular construction become tool popular in tier-1 and mega cities. It is easily designed and constructed on site in short period of time. Even, the modular construction building looks more innovative and attractive as compare to traditional buildings.
Let’s see what is it?
Table of Contents
What is Modular Construction
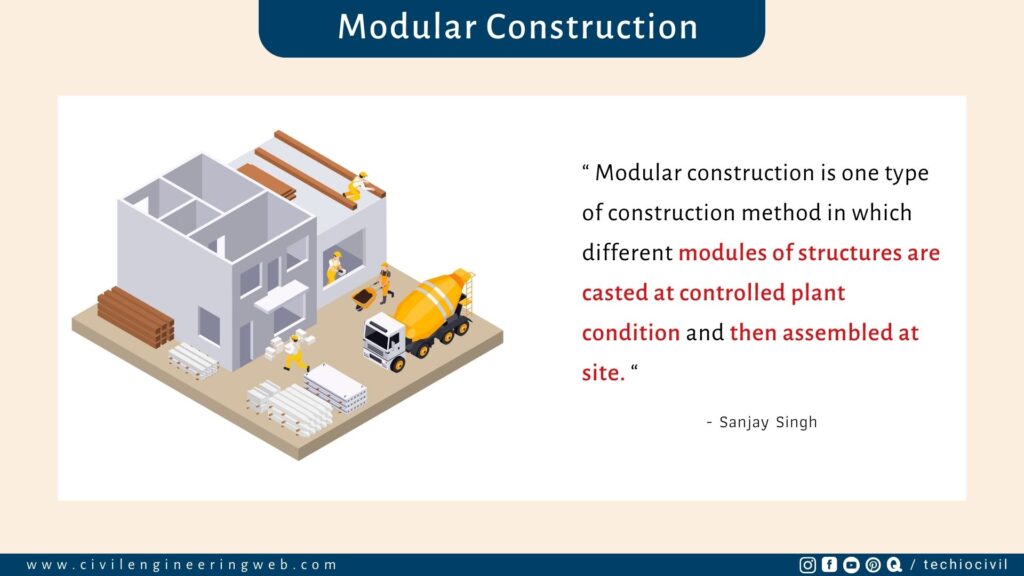
Modular construction is one type of construction method in which different modules of structures are casted at controlled plant condition and then assembled at site.
” Modules ” are the different part of structure or building that is connected by each other to complete the final structure.
As per the modular.org,
“The permanent modular construction industry grown 6.03% from 2.14% which is almost triple time growth as compared with 2015 in North America.”
The popularity of Modular construction building increasing rapidly due to its simple process, high quality construction and time saving.
Let’s see, the different advantages and disadvantages of modular construction which make it more popular.
Also Read: What is Monolithic Construction Technology
Advantages of Prefabricated Modular Construction
- Faster Construction
- High Quality Construction
- Safer Construction
- Limitless design opportunity
- Cheaper Construction
- Reduce Wastage of Materials
- Sustainable Construction
Faster Construction
It is one of the biggest advantages of modular construction. Due to off-site manufacturing of modules, the different process of construction can be done simultaneously which save the lots of construction time. Here are the few examples of time saving due to modular construction.
- Due to factory manufacturing, the delay due to weather is eliminated.
- Factory conditioned allows employees to work for more time to complete project in short period of time.
- The manufacturing of modules can be done simultaneously with site preparation such as construction of foundation etc. which save the 30% to 40% of construction time.
Also Read: What is Slurry Wall Construction
High Quality Construction
Due to factory manufacturing conditions, the casting of modules can be happened with high quality control. The material which is used to construct the modules can also be develop with high quality and quantity due to factory condition.
Safer Construction
Modular construction is a low-rise structure which is easily assemble by using machinery such as crane, only few labors are required to handle the assembling process of module on site which ultimately reduce the chances of accident.
Whereas in the manufacturing plant, a proper safety guidance, precaution and accessories is provided to employees which reduce the risk of accident.
Limitless Design Opportunity
Modular construction allow engineer to construct the structure in any design and shape with high quality.
Cheaper Construction
Modular construction saves the lots of construction time, labors requirement and material wastage which results the higher money saving and make construction more affordable.
Also Read: What is Shoring in Construction
Reduce Wastage of Materials
Due to factory Manufacturing conditioned, the materials are used precisely to construct the various modules. Also, the wastage can be easily recycled and reuse for other purposes.
Sustainable Construction
The modules of structure can be easily dis-assembled to reuse or relocate for other uses which reducing the demand of raw materials and minimize the amount of energy need to build new structure.
Also, the wastage of materials less as compared to traditional construction which reduces the impact on environment.
Disadvantages of Modular Construction
- Logistics
- Structural Approval from Authority
- Lack of Flexibility in Shape and Aesthetic
Logistics
Logistics is very important part of modular construction because the modules of structures are casted on factory, after the casting it is transported to the actual site by appropriate vehicle which become very crucial for modular construction.
Transportation of different modules need special attention and handling to deliver safely without any damage. Also, transportation of such modules increases the cost of transportation which sometimes become un-economical.
Also Read: Best Plants for Outdoor Garden
Structural Approval from Authority
Modular structure is totally different as compared to traditional structure due to which it needed additional attention in design to keep structure safe in various condition.
Its required additional calculation and assumption which sometime may different or unfollows the standard norm of traditional structure which make it too complicated to approve it from local approval authority. Authority needed the all calculation and proper source of assumption to approve it which affect the project timeline.
Lack of Flexibility in Shape and Aesthetic
Modular structure may be restricted to a uniform shape, style and design, as they are manufactured by mass production. As a result, they may lack aesthetic quality and convenient features from the customer’s perspective.
Let’s see the process or stages of modular construction of building.
Also Read: 9 Way to Remove Insects From Home
Construction Process of Modular Building
The construction process of modular buildings is very simple which is divided in five stages.

- Design Engineering
- Off-site Manufacturing
- Logistic
- On-site Manufacturing
- Site Restoration
1. Design Engineering
Design Engineering stage includes the conceptual planning and stability analysis of modular structures.
2. Off-Site Manufacturing
In this stage, the different modules of structures are fabricated on controlled plan conditioned as per design requirements
3. Logistics
In this stage, the different modules of structures are transported to the final location by appropriate machinery.
4. On-Site Manufacturing
In this stage, the different modules of structures are connected by proper arrangement to make a final product that is modular structure.
5. Site Restoration
The final stage of modular construction is the site restoration which includes treatment of land, land filling and cutting, landscaping, and other finishing work to make usable environment.
Also Read: 5 Best GPS Tracker for Construction Equipment
Types of Modular Construction
There are two basic types of modular construction.
- Permanent Modular Construction
- Temporary Modular Construction
Permanent Modular Construction
Permanent Modular Construction (PMC) is one best alternative of sustainable construction as I explain earlier. In this type of modular construction, the various modules of structures are fabricated on factory and then permanently fixed to actual location by appropriate manner.
It is suitable for single storey or multi-storey building with all services and good aesthetic appearance. It is a package of full functional building solution that could be constructed in short period of time.
Permanent Modular Construction Examples
1. Revival
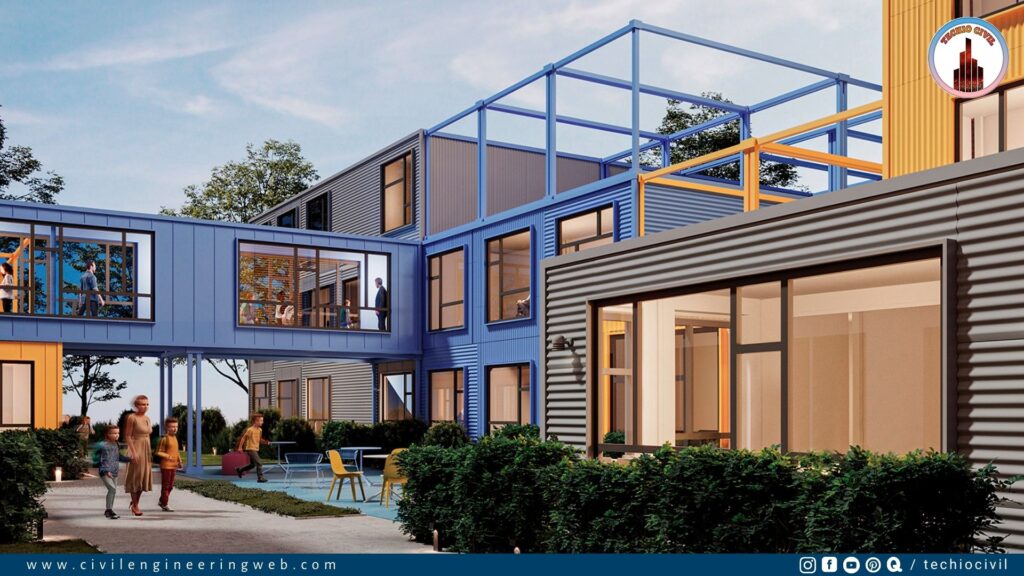
Function | School Building |
Architect | Zikzak |
Capacity | More than 175 Students |
Module Size | 3m x 6m & 3m x 9m |
Location | Ukrain |
Also Read: Deep Beam Design Criteria as per IS456
2. Nakagin Capsule Tower
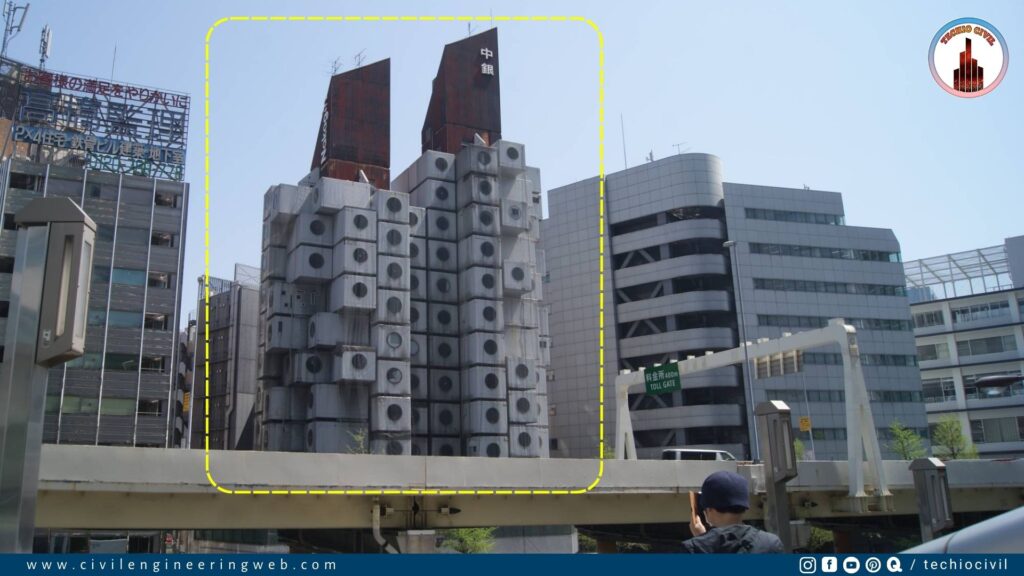
Function | Residential |
Architect | Kisho Kurokawa |
Module Size & Number | 4m x 2.5m & 140 Modules |
Location | Tokyo |
Also Read:
3. My Micro
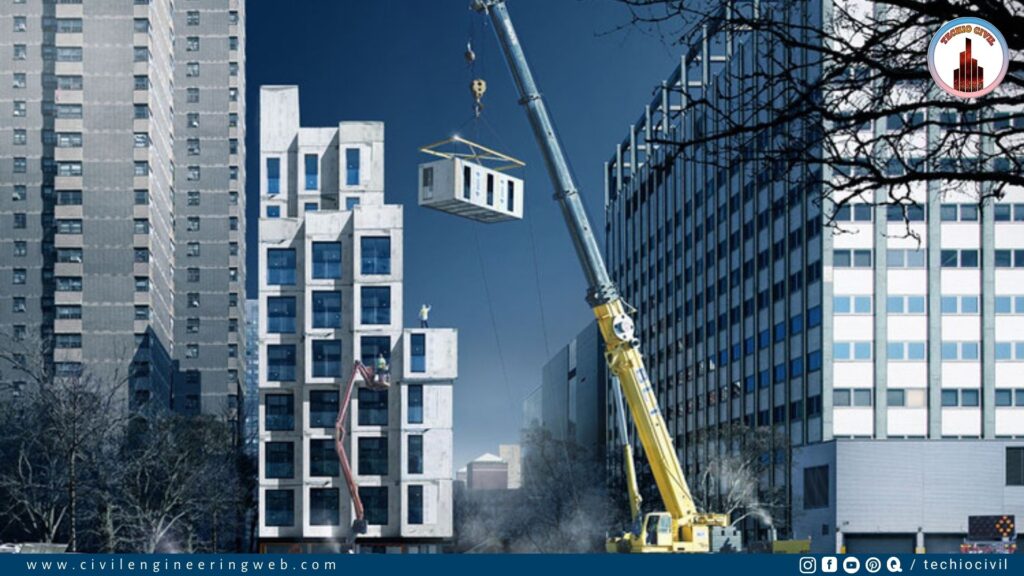
Function & Storey | Residential & 9 Storey Building |
Architect | nArchitects |
Module Number | 55 Modules |
Location | New York |
4. Wuhan Hospital
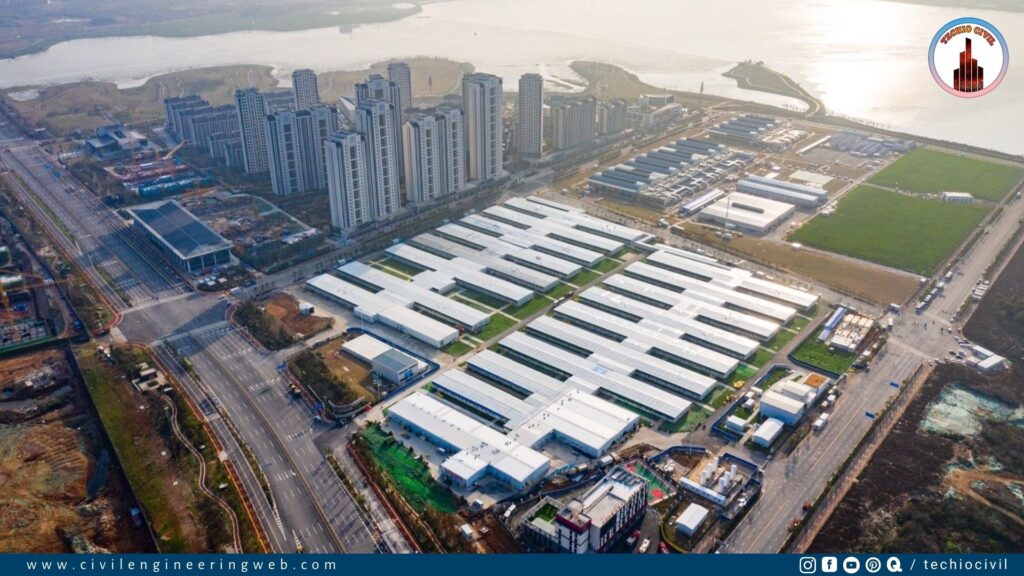
Function | Hospital |
Architect | nArchitects |
Construction Time | 2weeks |
Location | China |
Also Read: 3D Printing – Future of Construction
Temporary Modular Construction
In this type of modular construction, modular structures are designed to reused multiple times as per their uses and requirement on particular location.
A construction site office is perfect example of Temporary Modular construction (TMC) which is reused multiple times as per their requirement on site. If the construction work completed at any location, then the construction site office transported to other working site for reuse it.
Temporary or relocatable buildings are use for schools, construction site offices, medical clinics, sales center, etc.
FAQ of Modular Construction
What materials are used in modular construction?
Steel, Concrete, Wood, Aluminum, Plastic Composites, Roofing Material, etc. are used for modular construction as per requirement and durability of structure.
What are the disadvantages of modular construction?
Logistics, Structural Approval from Authority and Lack of Flexibility in Shape and Aesthetic are the major disadvantages of modular construction.
What are the benefits of modular construction?
Faster Construction, High Quality Construction, Safer Construction, Limitless design opportunity, Cheaper Construction, Reduce Wastage of Materials and Sustainable Construction are the major benefits of modular construction.
Can modular homes be moved?
Yes, Relocatable type of modular construction can be easily moved from one place to another place.
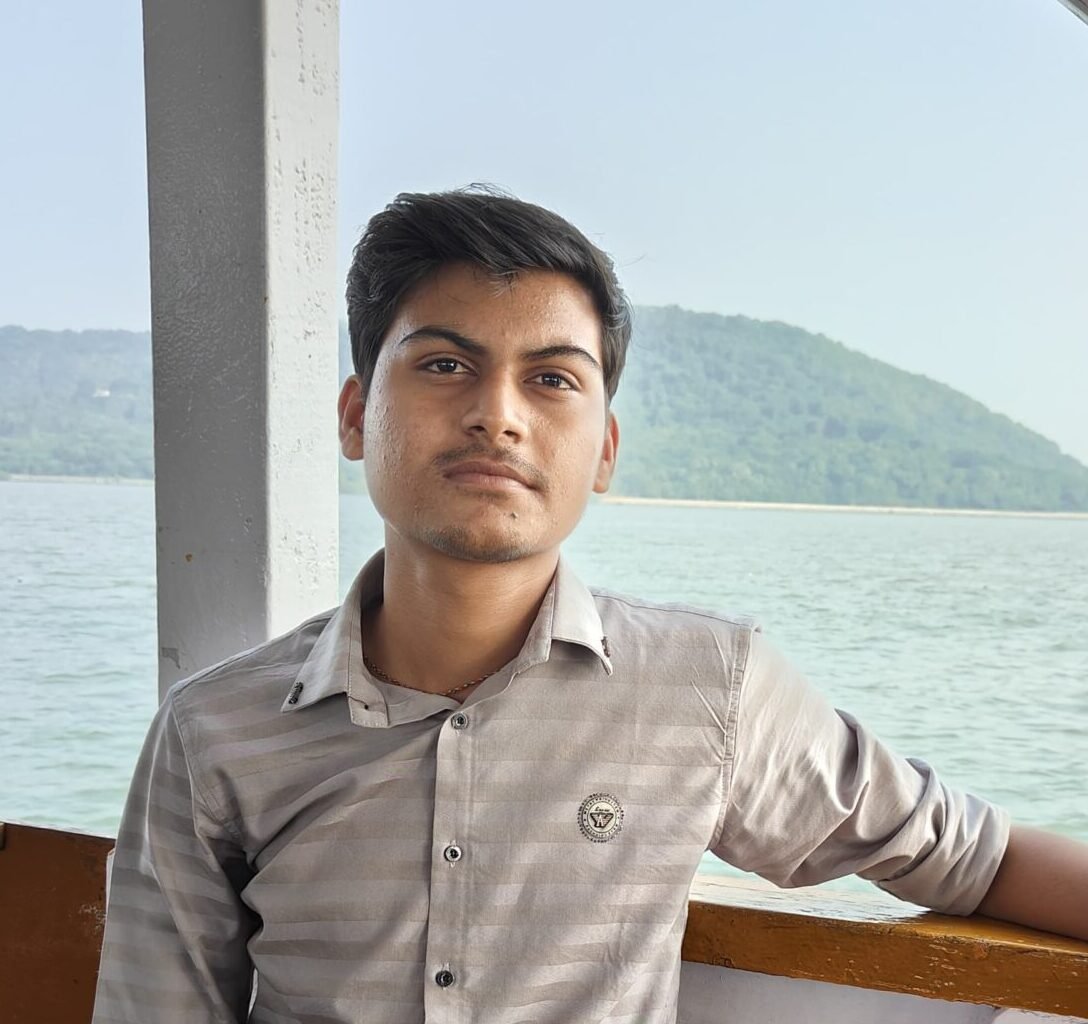
I am a Professional Civil & Structural Engineer having more than 4 years of experience in Engineering, Procurement and Construction industry. Here i sharing the latest updates of EPC Projects and Construction News.