In this article, We explain different special types of concrete. like fiber-reinforced concrete, high-density concrete, lightweight concrete, precast concrete, prestressed concrete, plum concreet, polymer concrete, No fine concrete, etc.
Table of Contents
Different Special types of concrete :
- Light Weight Concrete
- Plum Concrete
- Fiber Reinforced Concrete
- Polymer Concrete
- High Density Concrete
- Prestressed Concrete
- Precast Concrete
- Controlled Concrete
- Self healing concrete
- Fly ash concrete
- Silica fume concrete
- Self compacting concrete
- Transparent concrete
- Ready mix concrete
1. Light Weight Concrete:

Lightweight concrete is special types of concrete which have less weight and less density compare to other concrete.
The density of ordinary concrete is 2400 kg/m3. But light weight concrete has 400 to 2000kg/m3 density.
Light weight concrete can be prepared by in three main ways:
- Light Weight Concrete by using lightweight Aggregate
- Light Weight Concrete by introducing air bubbles (Aerated concrete)
- Light Weight Concrete by omitting fine aggregates (No – fines concrete)
Properties of light weight concrete:
Properties of light weight concrete are given below.
- Construction Density
- Compressive strength
- Tensile strength
- Thermal Insulation
- Fire Resistance
- Repairability
- Durability
Construction Density:
The density of light weight concrete is 400 to 2000 kg/m3. Low density light weight concrete used as thermal insulation material in building where high density light weight concrete used as structure block in building.
Compressive strength:
Compressive strength of light weight concrete is relatively high in its density. As the density increases the compressive strength increases from 0.5 N/mm2 to 35 N/mm2.
Tensile strength:
Its tensile strength is 15 to 20% of its compressive strength.
Thermal Insulation:
The Thermal Insulation of light weight concrete is three to six times more than of bricks and ten times more than of concrete.
Fire Resistance:
Light weight concrete has very good fire resistance and due to its low thermal conductivity, the building can be protected from the effects of fire.
Repairability:
Light weight concrete can be easily broken, cut, loosened. Thus construction can be easily repaired.
Durability:
Due to the porosity and low alkalinity of light weight concrete, it does not protect the iron from corrosion. Therefore, special processing is required to protect the iron from corrosion.
There are three types of light weight concrete as shown below.
- Light weight Aggregate concrete
- Aerated concrete or Cellular concrete
- No – fines concrete
Best book for Concrete Technology on Amazon
i. Light Weight Aggregate Concrete:
- This special types of concrete is made using lightweight aggregate instead of normal weight aggregate.
- The different lightweight aggregates are shown in Table.
- The compressive strength of this concrete ranges from 0.5 N /mm2 to 35 N/mm2.
Natural light weight aggregates | Artificial light weight aggregates |
---|---|
Pumic | Bloated clay |
Scoria | Expanded shale |
Rice husk | Sintered fly ash |
Saw dust | Artificial cinders |
Diatomite | Foamed slag |
Volcanic cinders |
Natural sand is added to improve the workability, strength and water requirement of light weight concrete to ensure that the concrete does not segregate during mixing.
Light weight aggregates increase water absorption. Thus aggregates can be coated with silicon compounds, which reduce water absorption.
The aggregate can also be coated with bitumen, but bitumen coating reduces the bond between the aggregate and the paste.
More concrete cover than normal concrete is provided to prevent corrosion of iron.
ii. Cellular Concrete OR Aerated Concrete or Foam Concrete:
- Cellular Concrete is a special types of concrete made by inserting air or gas bubbles into solid concrete.
- In India, such concrete is known by various trade names such as Siporex, Celecrete, Vayuthan.
Cellular concrete can be made in different ways as follows.
- By producing gas in concrete by chemical process.
- Adding foam to concrete
- Adding metal powder to concrete
Aluminium powder (0.2% by weight of cement) is commonly used as metal powder, metal powder combined with calcium hydroxide which is produced the process of hydration. This combination produces hydrogen gas in concrete.
Hydrogen peroxide and bleaching powder are also used for cellular concrete.
iii. No – fines concrete:
This special types of concrete does not use fine aggregate, only coarse aggregate, cement and water are mixed to make no-fine concrete.
- Particles smaller than 12 mm are not used in concrete.
- Single size aggregates are mostly used, which are passing through a 20 mm sieve and stopping at a 10 mm sieve.
- Single size aggregates have a higher porosity content which reduces the weight of the concrete.
- Aggregate/cement ratios in No fine concrete are usually kept from 6: 1 to 10: 1.
- The strength of no fine concrete depends on the water/cement ratio, aggregate to cement ratio, and density of concrete.
- Water cement ratios are kept from 0.38 to 0.52.
- The density is 1600 kg/m3 to 1900 kg/m3 if normal aggregate is used in no fine concrete but the density is 400 kg/m3 if light weight aggregate is used.
- The compressive strength of no fine concrete is lies between 1.4 N/mm2 to 14 N/mm2.
- No fine concrete has very low bond strength. Hence it cannot be used in RCC work. However, if it is necessary to use this concrete in RCC works, the iron rod will be cemented by the granulating process.
Advantages of light weight concrete:
Advantages of light weight concrete are as follows:
- As the dead load of the building decreases, the cross section of the building becomes smaller so that construction becomes economical.
- As the weight of the building decreases, the depth and cross-section of the foundation decreases.
- Construction speeds up, the cost of transportation decreases.
- Formwork has to undergo relatively low weight/pressure.
- The thermal conductivity of this concrete is higher than that of ordinary concrete. So, where air conditioning is to be used, it gives good weather and low power consumption.
- Light weight concrete can be easily nailed, easily cut, easily repaired.
- The use of light weight concrete increases the use of industrial waste such as clinkers, fly ash, slag etc.
2. Plum concrete:
Plum concrete is made for mass concrete using a large aggregate of a maximum size of 300 mm(called plums).
- In plum concrete, volume of aggregate kept similar to 20 to 30% of volume of concrete.
- Plum Concrete is also called cylopean concrete.
Plum concreting process:
- During concreting, the first layer of concrete is laid.
- The plums are then spread on it.
- A layer of concrete is laid on it again.
- Thus, one layer after another of concrete and plum comes.
- Since the concrete is relatively dry and hard, thus special type vibrators are used for adequate consolidation.
Heat of hydration is produced as large amount of concreting is done. Concreting is done in phases for short heights (0.1 to 15 mm), and a period of a few days is kept after each lift, so that the heat of hydration can easily dissipate.
Low heat cement should be used to reduce the heat generated during concreting.
Heat loss can be achieved by arranging pipes in concrete and carrying cold water in them.
3. Fiber Reinforced Concrete:

Fiber reinforced concrete is a special types of concrete that is prepared by mixing of concrete with additional fibers. Steel fibers, glass fibers, vegetable fibers, polypropylene, nylon, etc used in concrete.
- Plain concrete has very low tensile strength as well as ductility and resistance against cracks.
- If small fibers are mixed in such concrete, its tensile strength increases a lot. Such concrete is called fiber reinforced concrete.
- Fibers added to concrete reduce the workability of the concrete by winding around the aggregate. However, concrete mixes become more cohesive and less likely to segregate.
- Different types of fibers are used in this type of concrete. Such as steel, glass, polypropylene, nylon, asbestos, jute, coir. carbon etc. The fibers are rounded or flattened.
- The aspect ratio= Length of fiber/diameter is very important for fibers, which is around 30 to 150.
Fibers can be divided into two main parts:
Fibers Hard instrusion | Soft instrusion |
---|---|
Whose elastic modulus is greater than concrete. | Whose elastic modulus is less than concrete. |
Ex. Steel, carbon, Glass, etc. | Ex. Polypropylene, nylon, Vegetable fibers, etc. |
Concrete whose flexural and impact strength both are more. | Concrete whose impact strength is more but flexural strength has less. |
Steel fibers have more strength than nylon and polypropylene fibers. Round steel fibers are commonly used with a diameter of 0.25 to 0.75 mm.
Steel fibers increase the flexural, impact and fatigue strength of concrete. Steel fibers range from 1.0 to 2.5%.
Steel Fibers Rainforced Concrete (SFRC) is mainly used for highways, tunnel linings, bridge rails, hydraulic struts, earthquake resisting buildings, gutter covers, repair work, etc.
Steel Fibers Rainforced Concrete has a kinetic and shock resistance of 8 times to 10 times more than ordinary concrete. While tensile strength is doubled.
Factors affecting the properties of fiber reinforced concrete:
i. Type of fiber:
The modulus of elasticity of the fibers should be greater than the modulus of elasticity of the matrix. So that stresses can be effectively transferred between the matrix and the fibers.
ii. Fiber size:
As the total fiber size increases in concrete, the strength and resistance against impact increases. But if the fiber content exceeds 2%, the concrete becomes hard and segregation takes place.
iii. Aspect ratio:
Tensile strength and shock resistance increase if the aspect ratio of the fiber is up to 75 but tensile strength and shock resistance decrease if the aspect ratio exceeds 75.
iv. Placement of fibers:
If the fibers are Placed in the direction of the applied force, it gives greater tensile strength and shock resistance.
v. Size of coarse aggregate:
If the size of coarse aggregate exceeds 10 mm, the strength of concrete decreases.
4. Polymer Concrete:
Normal concrete is porous so its strength is low. Adding a polymer or a monomer to ordinary concrete reduces its porosity and increases its strength.
There are four types of polymer concrete:
- Polymer Impregnated Concrete (PIC)
- Polymer Cement Concrete (PCC)
- Polymer Concrete (PC)
- Partially impregnated and surface coated polymer concrete.
For more details of Polymer Concrete click Here: What is Polymer Concrete and Sulphur Infiltrated Concrete, Types, Application.
5. High Density Concrete:
The density of ordinary concrete is 2400 kg/m3, but the density of high density concrete is 3300 kg/m3 to 5500 kg/m3.
- The ordinary aggregates used in concrete has density is 2.6. But natural and synthetic aggregates with a density of about 4.0 are available.
- High density concrete formed, by breaking down magnetite or hematite or barite rocks containing heavy iron and using natural aggregates as suitable aggregates and fine aggregates of suitable grade. Hence we get 3500 kg/m3 density of concrete.
- If iron shots are used on both the site coarse aggregate and the fine aggregate. The density of the resulting concrete is as high as 5500 kg/m3.
- The compressive strength of such concrete is 20 to 21 N/mm2.
- Cement aggregate ratios are kept at 1: 5 to 1: 9 and water cement ratios are kept at 0.5 to 0.65.
Uses of high density concrete:
- For Radiation shielding.
6. Prestressed Concrete:
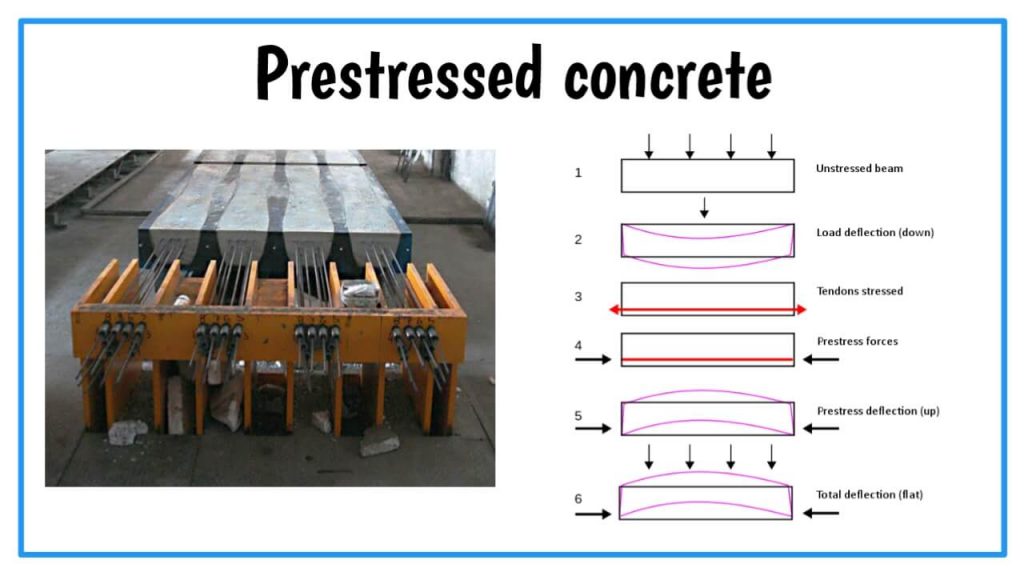
Prestressed concrete means to give a pre-calculated force or moment on structural member, so that the member is exposed to external loads, The resultant stress caused by the force or moment remains within its prescribed limits.
Simply prestressed concrete is a special types of concrete in which reinforcement bar are tensioned before embedded in concrete.
Click here to see Best books for Prestressed concrete on amazon
Advantages of Prestressed concrete:
- Tension crack can be prevented.
- Steel does not corrode.
- The size of the prestress section is smaller than the size of the RCC section.
- The weight of the structure decreases which results foundation cost decreases.
- Such concrete provides good resistance against Impact and Fatigue.
- The live load capacity of the beam increases.
- Such concrete is useful for Oil Wells and Nuclear Power Plants.
Disadvantages of Prestressed concrete:
- Requires high grade concrete (minimum M30).
- High grade steel is required.
- Good quality control is required.
- Formwork is intricate.
- Labor costs come high.
Types of prestressing:
- Pre – tensioning
- Post – tensioning
i. Pre – tensioning:
- In this method first formwork is prepared and wires (cables) are arranged in it.
- The cables are tied by pulling at both ends.
- Then concreting is done.
- Once the concrete has hardened, the cables are cut from both ends. So that the cables try to get shorter and compression are generated in the concrete.
ii. Post – tensioning:
- In this method poly pipes (ducts) are arranged from the profile in the right place in the formwork.
- Concreting is then done.
- Once the concrete has hardened, the cable is passed through a pipe and pulled to one end.
- Thus, in pre-tensioning, the cable is pulled before the concrete hardens while in post-tensioning the cable is pulled after the concrete hardens.
7. Precast Concrete:

Various components of concrete are cast before being used in the structure, dried and then used in the structure. Such concrete is called pre-cast concrete.
The different precast units are as follows:
- Solid concrete blocks
- Hollow concrete blocks
- Fencing posts
- Pipes
- Joists, beams
- Columns
- Floor and roof slabs
- Lintels
- Door/window frame
- Ventilators.
Such precast units are cast near the building site. It was then used in the building.
Precast concrete books on amazon
Advantages of Precast concrete:
- Quality control of structural element is good.
- Smooth surface is obtained.
- Concrete components like sand, gravel, cement do not need to be transported and stored on site.
- Even in bad weather precast units can be cast.
- Building can be done quickly.
Disadvantages of precast concrete:
- Special type of equipment is required for handling, transportation, lifting etc. of precast units.
- Skilled craftsmen and labour are required.
- Many precast units break down during handling and transportation.
- It is also difficult to assemble different components.
8. Controlled concrete:
Controlled concrete is defined as a special types of concrete which is prepared under good quality control and by taking consideration of design strength of concrete, workability, and durability.
- Controlled concrete is also called as Design Mix.
- For the Controlled concrete, different mixes are prepared and tested in the first laboratory using the proposed design method.
- The coarse aggregate and fine aggregate ratio and grading, water content, cement ratio, workability and capacity requirements are determined in this mix.
- Samples prepared in this way are tested in a laboratory.
- From the results, the required proportions of the components are modified, re-sampled and tested.
- This is how the design mix is prepared.
The strength of the concrete found in the laboratory and the strength on site are compared as follows.
Ft = Fck + K. S
where,
- Ft = target mean strength
- Fck = characteristic strength
- K = constant
- S = Standard deviation
9. Self Healing Concrete

Self-healing concrete is defined as the special types of concrete that is capable of repairing its self and gain its original position or back to its old position, due to water or air contact with un hydrated cement, further hydration occurs.
Self-healing concrete is introduced in the concrete which helps to repair the cracks by producing calcium carbonate crystals that block the micro-cracks and pores in the concrete.
The B. Pasteurii, Bacillus subtilis and B. Spharicus etc bacteria are use as self healing agent.
Click here to see more details of self-healing concrete : SELF HEALING CONCRETE ( BIO-CONCRETE)
10. Fly ash Concrete:
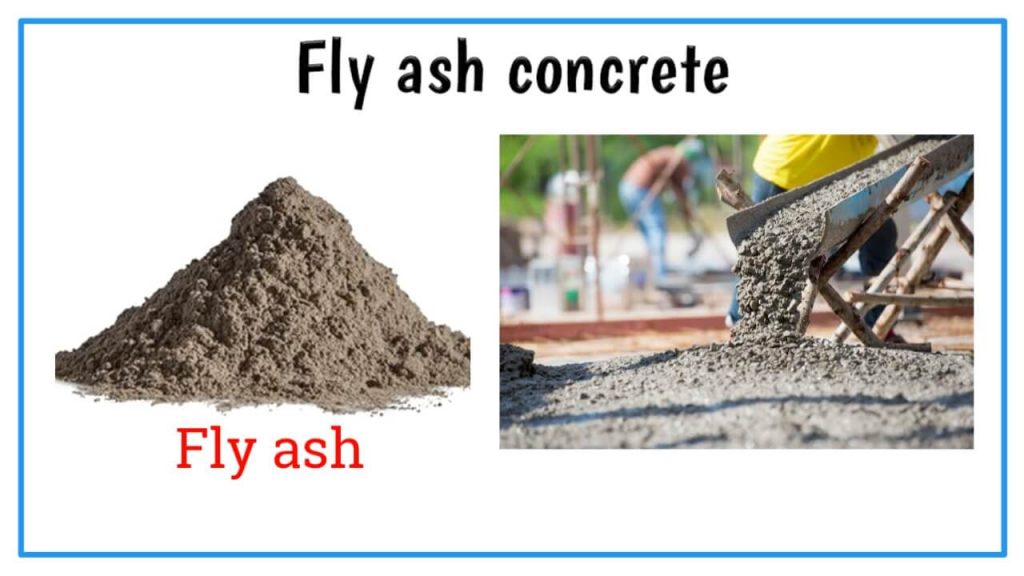
Fly ash concrete is a special types of concrete that are prepared by mixing concrete components with fly ash. Fly ash is generally obtained from power plants which is generated from coal.
Generally fly ash is used in concrete for the purpose of increasing the workability of concrete and as well as reducing the cement content in concrete.
As per IS:456-2000, Fly ash used in concrete up to 35% permitted by replacing of Ordinary Portland cement
11. Silica fume concrete:
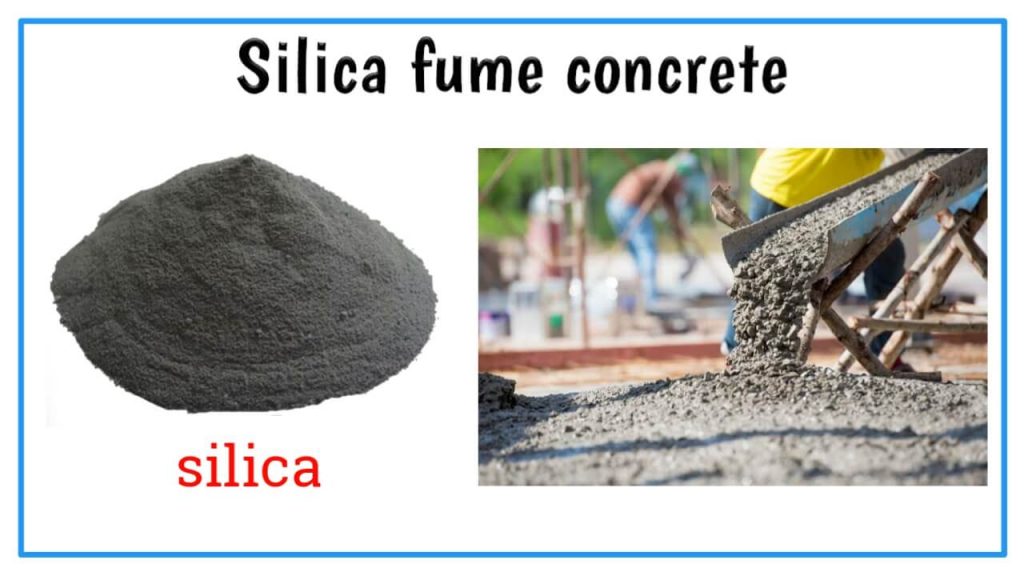
Silica fume concrete is a special types of concrete that is prepared by mixing of concrete components with silica fume. Silica fume is a by-product of silica. silica is also act as pozzolana material in concrete that means it also affects the concrete strength.
Advantages of adding silica fume to concrete:
- Use As a part of cement (0 – 10%).
- Ultra high strength concrete making (Strength 70 to 120 MPa).
- To control Alkali – aggregate reaction.
- Increase the starting strength of Fly ash/slag cement
- to suppress sulfate attack.
12. Self Compacting Concrete:
Self compacting concrete is a special types of concrete that flow under its own weight and fill space of formwork without need for Mechanical vibration. It is also known as flowing Concrete.
Self compacting concrete is used where compaction of concrete is difficult by various mechanical vibration devices.
13. Transparent Concrete:
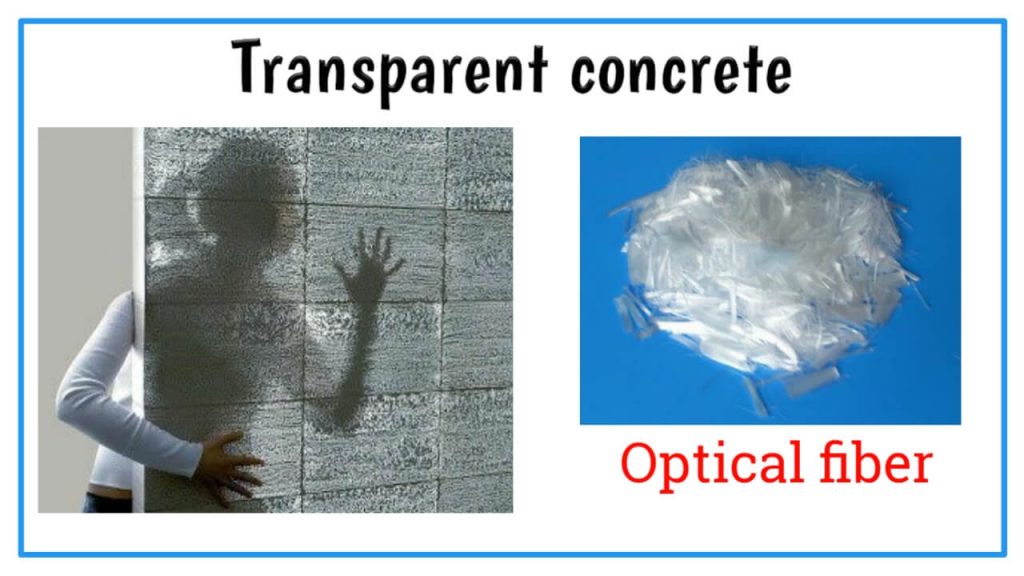
Transparent concrete is a Special types of concrete which allows pass light through it. Transparent concrete is also known as light-transmitting concrete or translucent concrete.
Light transmitting through concrete Due to some amount of coarse aggregate content of concrete is replace with light-transmitting material or optical fibers.
In this concrete, the high amount of fine aggregate is used or fine material is used.
Transparent concrete is similar to ordinary concrete because the strength of both concrete is similar. But the major disadvantage is the transparent concrete is costly compare to ordinary concrete.
For more details of transparent concrete click here: What is transparent concrete? Material used || Advantages and Disadvantages.
14. Ready mix concrete:

Ready mix concrete is a special types of concrete that is prepared at ready mix plants and transport from to construction location.
Ready mix concrete is good quality of concrete because it is prepared under good quality of control and the content of aggregate, sand, and water is also well specified as per design mix of concrete.
Ready mix concrete is transported by transit mixer.
Also read:
- How many types of chemical admixture used for concrete
- Common Types of Concrete Repair Mortar, Chemicals and other Repair Material
- 8 Aspects to Make Earthquake Proof Masonry Construction
- What is Ferro cement? Material, Construction Method, Application, Uses.
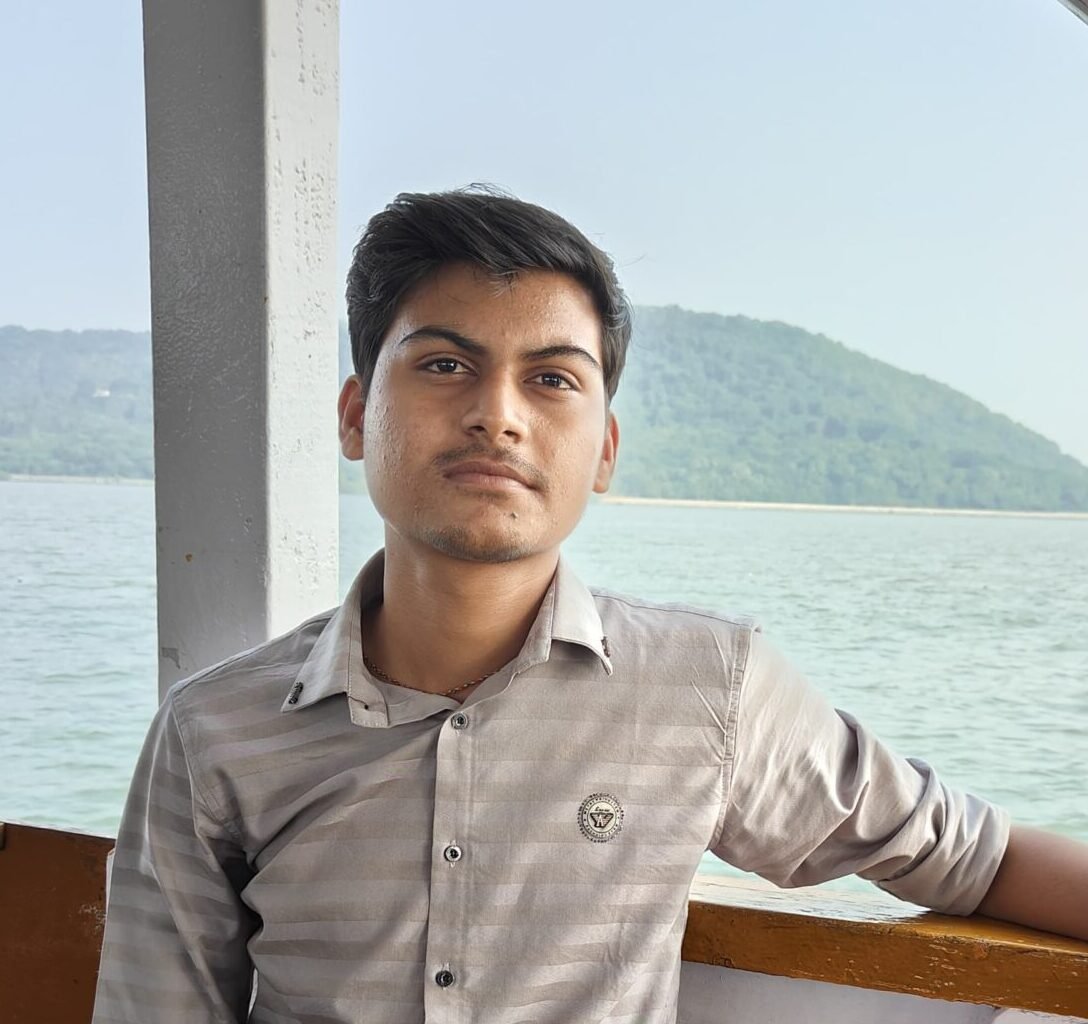
I am a Professional Civil & Structural Engineer having more than 4 years of experience in Engineering, Procurement and Construction industry. Here i sharing the latest updates of EPC Projects and Construction News.