we share Important points to check quality of construction material like, how to check quality of cement, aggregate, bricks and water. how to check quality of cement on field py performing simple task. Important points are remember while storing cement. field test on aggregate, water, bricks to check its quality. because quality construction is achieved by material quality.
Table of Contents
How to check quality of construction materials:
Many types of materials are used in civil engineering constructions for various activities. therefore factors affects the quality of construction are as below.
Factors affecting the quality of construction:
- Quality of materials used in construction such as cement, steel, sand, gravel, water, bricks, etc.
- Cement-sand-gravel ratio
- Water/cement ratio (w/c ratio)
- Workability
- Curing
- Quality of machinery used in construction e.g. Mixer, Vibrator
- Method of construction and speed of work: Excessive work speed reduces the quality of construction.
- Skills and experience of labor
- Design of construction components
- Mistakes made during construction
- Construction supervision
Important Point To Check Quality of cement:
Cement is the most important material used in construction. It is used in almost every item of construction. The function of cement is to strengthen it by adding sand and gravel.
Cement is used in the following construction items.
- Concreting work
- Plastering work
- Masonry work
- Flooring work
- Grouting work. Etc.
There are two main types of testing, for cement quality.
- Field testing
- Laboratory testing
Field testing:
Field testing is sufficient when cement is to be used for a small construction or for less important construction. There is no special need for laboratory testing
How to check quality of cement on a field.
- The bag of cement should be machine sewn.
- It should weigh 50 kg.
- The color of the cement should be uniformly greenish gray or brown.
- The cement should feel cold when you put your hand in the cement bag.
- Cement bag should not have lumps.
- The cement should feel smooth to the touch. Sandy or clayey cement looks gritty.
- A handful of cement should be floated in water for a while.
- Make a water-thick paste in about 100 gm of cement. Make a sharp-edged cake out of it. Place the cake on a glass plate, gently place the plate in a bucket filled with water. The shape of the cake should not change while taking the plate down into the water. After 24 hours, the cake should retain its original shape as well as gain a little strength.

Laboratory testing:
When cement is to be used in an important construction or in a large space, the quality of cement cannot be determined on the basis of field testing alone. In such a case, it is very important for the cement user to undergo laboratory testing of the cement.
Cement is subjected to laboratory testing for its following properties:
- Fineness
- Consistency
- Setting time
- Compressive strength
- Soundness
- Heat of hydration
- Chemical composition
Cement Quality Requirement as Per I.S. Code
Sr.no | Test | Purpose | I.S. Requirement |
1. | Fineness | Determining the Fineness of Cement Particles | For OPC 53 GRADE As per I.S 12269-1987 1. The weight of the residue should be no more than 10% for OPC and not more than 5% for Rapid Hardening Cement after 100 g of cement has been sieving for 10 minutes from 90 (I.S, sieve No, 9). 2. Specific surface area according to air permeability test, for OPC should not be less than 2250 cm2/gm and for RHC note less than 3250 cm2/gm. |
2. | Setting Time | To determine initial setting time of cement. To determine final setting time of cement. | Initial setting time OPC – 30Min RHC – 30Min Low heat cement – 60Min Final setting time Not less than – 600Min |
3. | Compressive Strength | To determine compressive strength of cement. | For OPC (53 grade): 3days – 27 N/mm2 7days – 37 N/mm2 28days – 53 N/mm2 For RHC : 3days – 27 N/mm2 For High Alumina Cement: 3days – 35 N/mm2 |
4. | Soundness | To determine the expansion of cement after setting. | 1. Expansion Not more than 10mm in Le-chtelier test. 2. Expansion not more than 0.8% in Autoclave test |
Points to keep in mind while storing cement:
- Store rooms floor, walls, roof etc. should be waterproof.
- Windows and the number of doors should be kept minimum.
- The level of plinth should be higher than the ground level.
- Cement bags should be kept 30 cm away from the wall.
- Kept 14 bags in one column of cement row. That Means the height of cement bags row should not exceed 14 bags,
- Cement bags should be placed on the floor in a damp area with wooden planks.
- Old bags should be used first.
- To reduce air circulation between the cement bags, space should not be kept between the column of cement bags.
- Cement should not be stored for a long time.
Important Point to Check Quality of Bricks:
Brick is also an important building material. Bricks are usually made from clay or by mixing Fly ash with clay. It is commonly used in the following items of construction.
- Bricks in flooring
- In columns
- In masonry of walls
Bricks are usually used to withstand compressive loads.
Tests for quality of bricks :
- Bricks should be well baked. Its color should be a uniform dark night.
- The Edges of bricks should be uniformly sharp.
- Bricks should not be broken from a height of approximately 1.2 m.
- A metallic ringing sound should be produced when two bricks collide with each other.
- Brick surfaces should be hard enough. Scratching brick surface with the Help of finger nails scratch impression not left on brick surface.
- When breaking a brick, its texture should be uniform and compact.
- There should be a “frog” on the top surface of the brick, so that the grip is maintained between the upper and lower two layers of masonry.
Size of brick:
The standard size of a brick should be as follows.
- Standard size:19 cm x 9 cm x 9 cm
- Modular Size: 20cm x10cm x10cm.
- bricks should weigh 2.7 to 3.1 kg. According to I.S. another standard size of brick is 19 cm x 9 cm x 4 cm which is not very Popular.
- After cleaning the sides of the brick, the length of the 20 bricks Should be according to Below.
1st class brick | 2nd class brick | |
Length | 368 to 392cm | 350 to 410cm |
Width | 174 to 186cm | 165 to 195cm |
Heigh | 174 to 186cm | 165 to195cm |
Water absorption of Bricks: (IS ; 1077 -1976)
After immersed Brick in water for 24 hours,
- Water absorption of first class bricks should not absorb more than 20% water.
- Water absorption of second class bricks should not absorb more than 22% water.
- Water absorption of third class brick should not absorb more than 25% water.
Compressive strength of Brick:
- Compressive strength of First class brick :7.0 N/mm2 to 14 N/mm2
- Compressive strength of Second class brick: 7.0 N/mm2 to 3.5 N/mm2
- Compressive strength of third class brick: less than 3.5 N/mm2
Efflorescence test for brick:
- This test is done to find out the alkali content in bricks.
- Arrange 5 bricks in a dish so that they stand on top of each other.
- Fill this dish with distilled water to a depth of 2.5 cm.
- Leave the dish open in the air at a temperature of 20 to 30.
- When all the water has evaporated again fill the dish to a depth of 2.5 cm.
- Observe the bricks when all the water has evaporated.
Observation | Result |
No perceptible deposit | Nil – efflorescence |
10% area covered with thin deposit of salts | slight – efflorescence |
50% area covered with deposit of salts without flaking of surface | Moderate – efflorescence |
50% area covered with deposit of salts with flaking of surface | Heavy – efforescence |
Important Point to Check Quality of Aggregate:
- There are two main types of aggregate. Fine aggregate and coarse aggregate
- Aggregates are smaller than 4.75 mm is known as Fine aggregate.
- Aggregates are larger than 4.75 mm is known as Coarse aggregate.
- According to I.S : 383 -1970 Natural aggregates should be the first choice.
- Grading limits of Fine Aggregate according to I.S : 383 -1970, table – 4 years
- The amount of flaky and elongated particles should be less in Coarse Aggregate.
- The fineness modulus (F.M.) for Fine aggregate should be between 2 to 3.2.
- The fineness modulus (F.M.) for Coarse aggregate should be between.5.5 to 8.0.
Fineness Modulus | Classification |
2.2 to 2.6 | Fine sand |
2.6 to 2.9 | Medium sand |
2.9 to 3.2 | Coarse sand |
- Content of Na2O in a aggregate volume, should not exceed 0.06%.
- The aggregate should be hard, strong, durable, clean and free from veins.
The limit of deleterious materials in aggregate should be as follows.
Deleterious material | Fine Aggregate % by weight | Coarse Aggregate % by weight | ||
Uncrushed | Crushed | Uncrushed | Crushed | |
Coal & Lignite | 1% | 1% | 1% | 1% |
Clay Lumps | 1% | 1% | 1% | 1% |
Particles size <75µ | 3% | 15% (not considered in total) | 3% | 3% |
5% | 2% | 5% | 5% |
Important Point to Check Quality of Water:
The water used in construction is chemically react with cement. Water is used to make concrete or mortar. Water is also used for curing.
Water has the following impurities.
- Organic,
- Salt (Inorganic)
- Sulphates
- Alkali chlorides
Impacts of impurities on concrete properties:
- If water have high dissolved salts then Compression strength of concrete is reduced by 10 to 30%.
- Dampness and efflorescence occur when water contains high levels of chlorides (e.g. seawater).
- Corrosion of iron rods by sea water.
- Sodium and Potassium carbonates lead to faster setting of cement and if in large quantities the strength of concrete decreases.
- Calcium chloride accelerates the setting of cement.
- Water algae reduces the grip between the cement and the aggregate and increases the amount of air in the concrete to reduce the strength of the concrete.
- If the sugar content in the water is more than 0.20%, the setting is done quickly and the strength of after 28 days is reduced.
- Inorganic salts such as manganese, tin, zinc copper, lead etc. reduce the strength of concrete.
- Silt and suspended particles interfere with the setting of the cement.
The maximum amount of impurities in water for making concrete is as follows:
Types of Impurity | Maximum Amount (mg/lit) |
Organic | 200 |
Inorganic | 3000 |
Sulphates | 400 |
Alkali chlorides Plain concreteReinforced concrete | 2000500 |
Suspended matter | 2000 |
- Potable water is required for construction.
Also Read:
- Classification of Aggregates Used In Construction Work
- 3 Major Components of Quality Control of Ready Mix Concrete
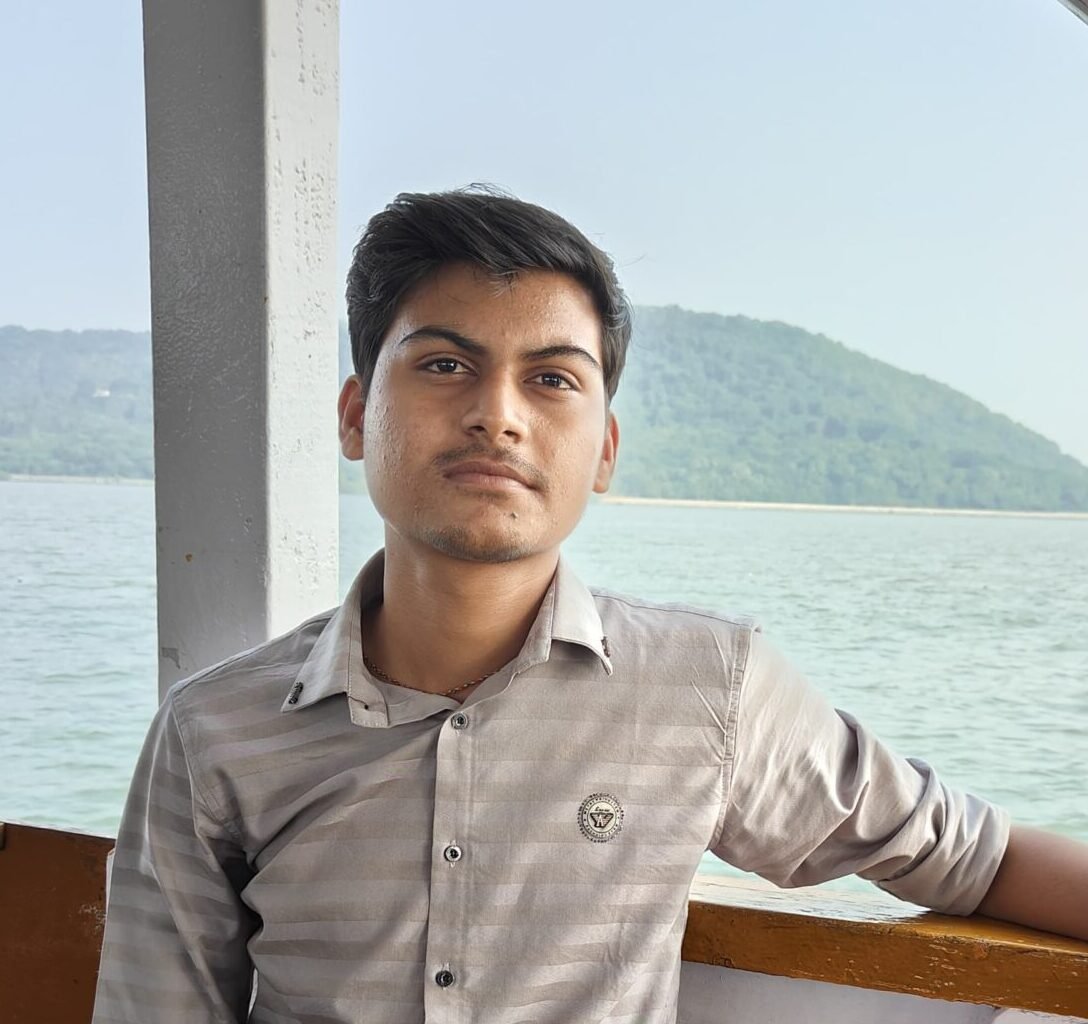
I am a Professional Civil & Structural Engineer having more than 4 years of experience in Engineering, Procurement and Construction industry. Here i sharing the latest updates of EPC Projects and Construction News.